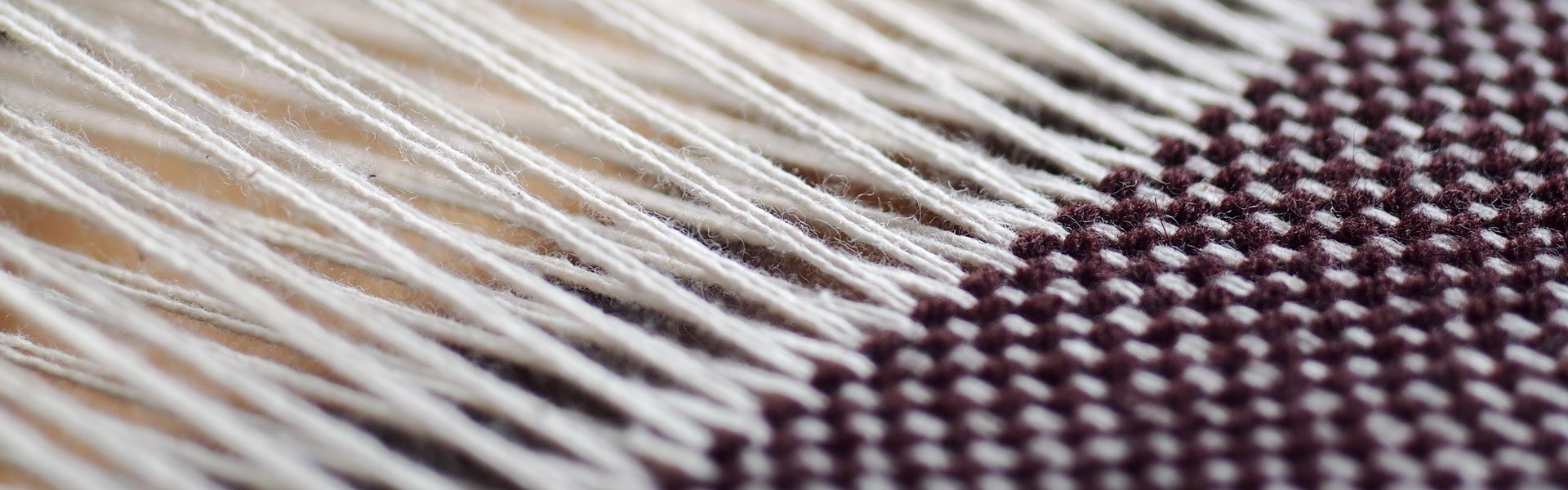
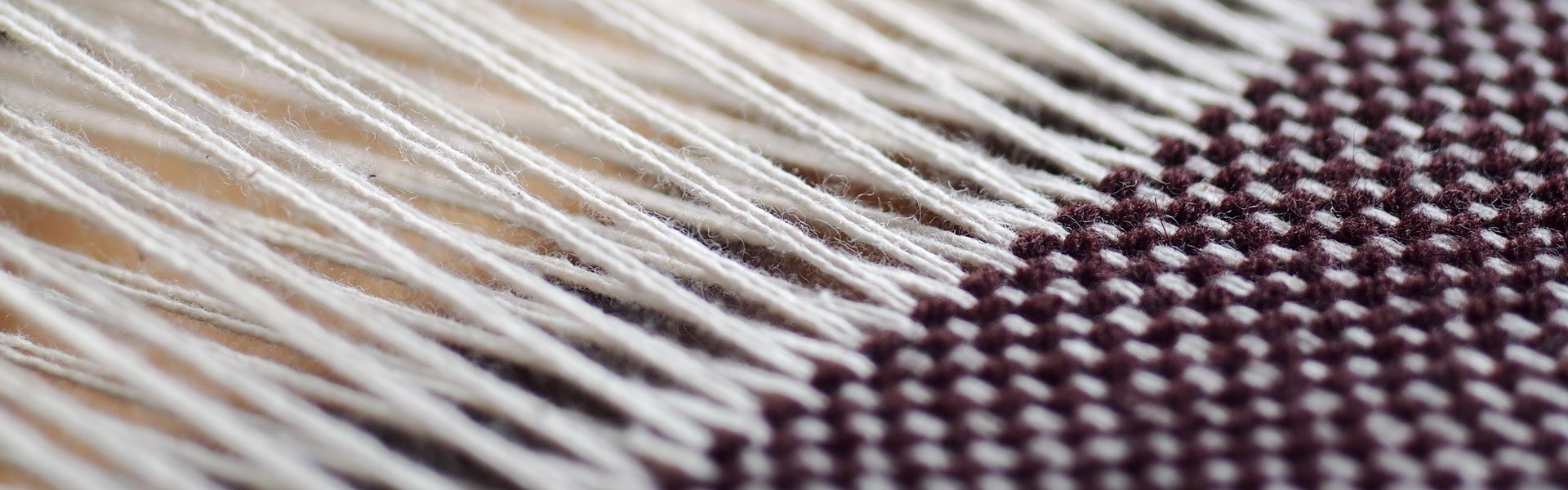
- Home
- Applications
- Weaving
Weaving Preparation
Weaving Preparation
Optimizing Air Quality and Efficiency in Warping Rooms.
Efficient air management in the warping process is crucial for maintaining yarn quality, minimizing fiber loss, and ensuring a clean, controlled environment for textile production. Luwa Air Engineering brings decades of expertise to create highly efficient air conditioning and filtration systems specifically designed for warping rooms in weaving preparation.
Why Warping Demands Uncompromised Air Management
The high-speed operation of warping, where thousands of individual yarn ends are meticulously wound onto a warp beam, is highly susceptible to environmental variations. Without precise control, you face significant challenges that directly impact your profitability:
- Costly Yarn Breakages & Defects: Inconsistent temperature and humidity levels can cause yarn to become brittle, sticky, or uneven. This leads directly to frequent yarn breaks, uneven tension, and defects that propagate through the entire production chain, resulting in costly reworks and material waste.
- Disruptive Static Electricity: Uncontrolled static electricity is a major headache. It causes yarn to cling, tangle, attract airborne contaminants, and severely disrupting smooth production flow and leading to significant downtime and material losses.
- Harmful Lint & Dust Accumulation: Warping machines generate substantial amounts of fiber fly and dust. If not effectively removed, these particles can pollute the yarn, clog sensitive machinery sensors, accelerate wear and tear, and create an unhealthy, uncomfortable working environment for your operators.
Key Luwa Components for Warping Room Air Management
Luwa’s air engineering systems for warping rooms are built on a foundation of robust, industrial-grade components designed to ensure superior air quality, continuous operation, and minimal fiber contamination. From the Rotary Pre Filter (RPF) and Rotary Drum Filter (LDF) for efficient dust and fiber extraction, to the Modular Central Filter (MCV) and Fine Dust Filter (FDF) for advanced air purification, each component plays a vital role. The Waste Separator (WSA) enhances sustainability by managing fiber waste, while the Luwa Air Washer ensures precise climate control to protect yarn integrity. Finally, B600 Axial Flow Fans deliver optimal airflow with energy efficiency and low noise. Together, these components form a complete, reliable solution tailored for high-performance warping room environments.
Benefits of Luwa's Warping Room Solutions
Luwa’s advanced systems deliver measurable improvements in yarn quality, operational efficiency, and workplace safety—while supporting sustainability and cost savings.
- Enhanced Yarn Quality and Beam Consistency: Luwa systems create the ideal climate for yarn handling by maintaining precise temperature and humidity. This minimizes yarn brittleness, stickiness, and tension irregularities. With a static-free and clean environment, warp beams remain uniform, defect-free, and production-ready.
- Improved Operational Efficiency and Machine Uptime: Stable environmental conditions significantly reduce yarn breaks and machine stoppages. With automated filtration and waste removal, maintenance frequency drops while production throughput increases—leading to greater efficiency and lower operational interruptions.
- Cost-Effective and High Return on Investment (ROI): Lower yarn breakages and reduced material wastage translate to substantial savings. Luwa’s energy-efficient systems cut power consumption while extending machinery lifespan. Automated waste handling also reduces the need for manual labor, freeing up skilled workers for more valuable tasks.
- Superior Worker Health, Comfort, and Safety: Luwa's advanced filtration systems ensure clean air, free from lint and micro-particles. By maintaining comfortable temperature and humidity levels, the systems reduce heat stress and respiratory risks, leading to healthier and more productive working conditions.
- Environmentally Responsible and Sustainable: By enabling effective fiber reclaim and reducing energy usage, Luwa supports your sustainability goals. The system’s efficient design helps cut carbon emissions and minimizes environmental footprint without compromising performance.
- Reliable Performance with Global Support: Every component in a Luwa system is engineered for durability in industrial environments. Backed by decades of experience, Luwa offers full after-sales support and global service availability to ensure your air system performs optimally year after year.
Backed by 90+ Years of Global Experience
Luwa is a pioneer in textile air engineering, with thousands of successful installations around the world. Our warping room solutions are tailor-made to suit your production needs, plant size, and budget—backed by on-ground technical support and after-sales service.
Whether you're modernizing an existing plant or building a new one, Luwa has the experience and engineering know-how to deliver high-performing, cost-effective air systems.
Ready to explore a better air solution for your warping room?
Contact Luwa today to request a site visit, consultation, or custom system design.