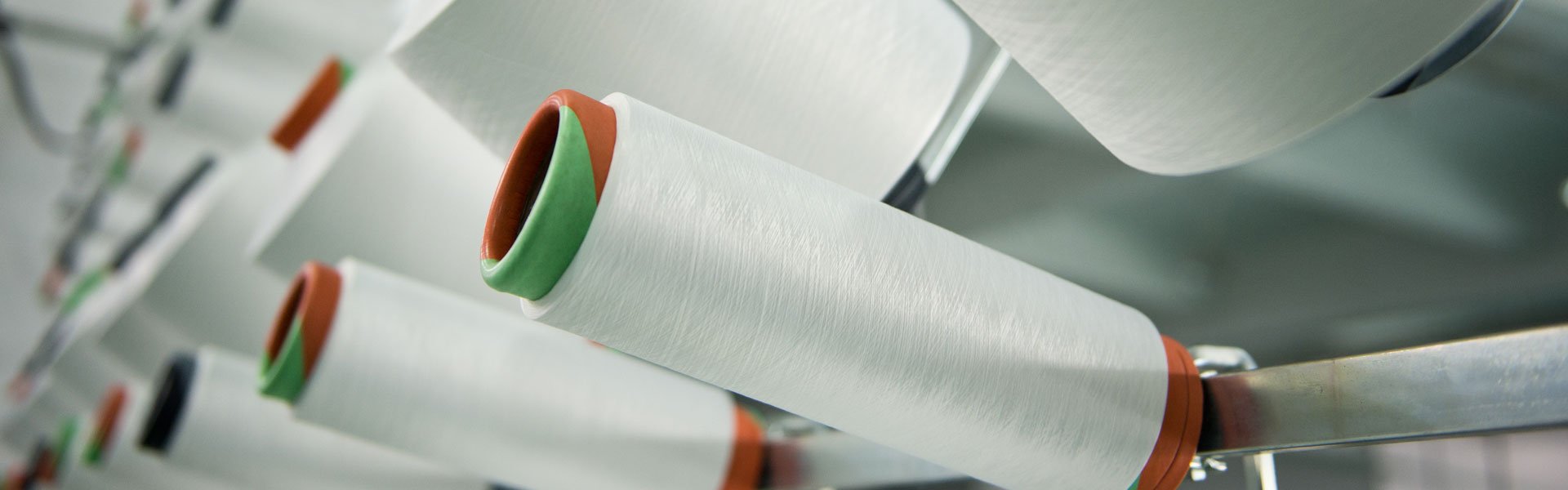
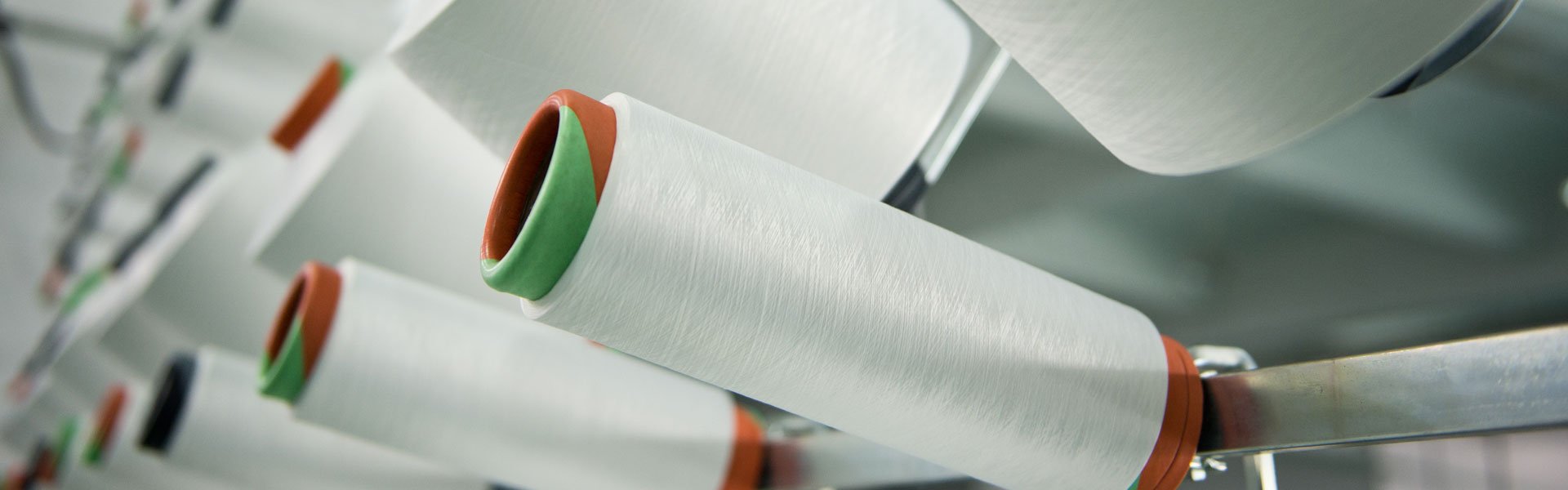
- Home
Sub page
Sub page
Maintaining the correct humidity level is essential for smooth machine operation. Moisture reduces electrostatic charges, especially on synthetic fibres. But higher humidity increases lapping and reduces the effectiveness of disentangling and alignment. Also, breaking forces and elongation are directly influenced by the ambient humidity in the department. Optimum values vary depending on the use of the raw material and its mixture. A higher relative humidity will result in a lower room temperature during the evaporative cooling mode.
Fibre Recovery and Disposal - Most spinning preparation machines have integrated suction points that can be incorporated into a fibre deposit system. The fibre separation and dust filtration plant must be designed in such a way that it can handle the required air volume and also the amount of waste fibre.
Depending on the raw fibres used in the plant, several fibre separators can be installed to separate the different materials from each other.
Modern fibre depositing plants are integrated with bailing press systems to automatically store and bale different qualities of waste fibres. This reduces personnel costs and increases the efficiency of the bale press.
The dependency on the fibre depositing system is essential for the operation of the mill. A standstill of either the fibre depositing plant or the bailing system leads to an immediate shutdown of the entire spinning mill.
Fibre Fly / Dust Contamination - In order to prevent unwanted infiltration of dust from the outside, the mill is kept at constant overpressure. Depending on the outside air contamination, fresh air filters and, depending on the process requirements, supply air filters are required. Local regulations may set Permissible Exposure Limits (PEL) to protect textile workers from byssinosis. Sufficient air changes throughout the mill are required to dilute the dust levels and keep the departments clean and free of fly liberated from the machines.
Not all industrial processes are equally sensitive to temperature fluctuations. For example, quenching air processes are highly sensitive and must be controlled within a narrow range.
However, all processes prefer a constant temperature, as most nonwoven raw material are hydrophilic and the moisture absorption capacity changes with temperature. In addition to reducing quality variation, temperature control has a positive effect on:
- reduced fibre fly in the mill,
- fewer electronic failures of the machine control system and
- a better working environment for the employees.
Daily room temperature fluctuations can be minimized by using refrigerant cooling instead of evaporative cooling, especially during the summer months and monsoon rains.